Autoclaves for vulcanisation
Olmar ATV vulcanising autoclaves are mainly used in the rubber industry although they also play a role in the consolidation processes of other materials such as steel or plastic.
The use of these autoclaves is widespread in various sectors such as the automotive industry (mainly in relation to the vulcanisation of tyres), the naval industry (manufacture of boat and dock rubber fenders and accessories), the design of roller and belt conveyors and the vulcanisation of complementary parts (tubes, hoses, gaskets, etc.). This wide variety of markets makes Olmar ATV vulcanising autoclaves one of the most demanded pieces of equipment both nationally and internationally.
The whole process is fully automated thanks to the new Olmar OCS software, which was developed entirely by Olmar engineers and makes it possible to control, study and take action on all of the variables of the cycle in real time. This modern system ensures an optimum end result, and also makes it possible to develop different work, monitoring and control programmes tailored to the different needs of each customer.
- Industries
- Other Autoclaves
The use of vulcanised rubber in the most technologically advanced industries has become widespread over recent years, evolving from an accidental discovery to unprecedented industrialisation in the automotive sector at the start of the 20th century.
Let’s take a quick look at its history: one night in 1839, Charles Goodyear left natural rubber mixed with sulphur on a hot plate. By the following morning, the rubber had turned into elastic rubber, having completed the first ever rubber curing cycle. This process was patented by Mr. Goodyear in 1843 (but also by Mr. Thomas Cook in the UK, leading to different theories about its invention).
As heat and sulphur had been associated with the god Vulcan, the process came to be called vulcanisation.
Vulcanisation in an autoclave is a chemical process applied to rubber and other natural compounds with elastomeric properties, which makes it possible to increase their elasticity and decrease their plasticity, thereby improving their mechanical, physical and performance properties such as hardness, viscosity and strength (mainly tensile strength and resistance to weathering).
Olmar ATV vulcanising autoclaves accelerate these processes, making it possible to safely and optimally convert natural rubber and plastic (synthetic rubber) into cured parts and products.
With applications in countless sectors and industrial processes, the exponential growth of autoclave-cured rubber is mainly determined by its use in:
Products / Autoclave for vulcanising of natural and processed rubber / Autoclaves and natural and processed rubber
- Coating and retreading tyres for heavy vehicles, such as trucks and off-road vehicles (ORT - off-road tyres)
- Coating and retreading passenger car tyres (SBR - styrene butadiene rubber)
- Coating of rollers on conveyor belts
- Coating of rollers in printing presses
- The manufacture of rubber seals for the automotive, aviation and shipping industries, radiator hoses, cables and spark plug caps (EPDM rubber).
- Electrical applications such as the insulation of high-voltage cables
- Sheathing of high-temperature cables
- The manufacture of low, medium and high pressure rubber hoses and sleeves
- The manufacture of protective rubber covers where thermal resistance to ozone, weathering, corrosive chemicals and oils are essential properties.
- Curing of seals and O-rings
- Others such as mats, boots, etc.
These products, which have been improved thanks to the autoclave treatment process, will be used in abrasive conditions and/or in extremely corrosive environments, and their life cycle will have extended and their performance will have improved as a result of this process. In general, this result cannot be achieved by standard press-based compression moulding.
The autoclaves for vulcanising rubber manufactured by Olmar (called ‘ATV’) are not only notable for their high level of technological development, but also for their reliability and durability, which ensure the best performance and highest levels of efficiency throughout their useful life. The application of rubber in increasingly critical manufacturing elements has brought with it an exponential increase in the demands for testing the control, fatigue and measurement of this equipment. Only the most advanced autoclaves are capable of ensuring the levels of homogeneity and cycles required by the industry, which is why it is increasingly important to invest in R&D and constantly improve them.
In this sense, since it started its activity in this sector (the company represented Uniroyal in Spain for more than 15 years in the 1970s), Olmar has dedicated a large part of its resources and R&D to researching the possibilities of these new materials, and has become a national and international benchmark in their study and industrial application.
Rubber vulcanisation cycle
As mentioned above, rubber is basically an elastomer that can be either natural or synthetically produced (made in petrochemical plants by chemical synthesis), and then vulcanised in an autoclave to improve its physical and structural properties.
Once it has been put into the autoclave, in a standard cycle, rubber must reach a temperature of 170ºC (350ºF) and a pressure of 6 BarG (90 psi), and stay at this temperature and pressure for a pre-set time. These conditions may vary depending on the type of rubber and its application.
It is essential to correctly define the maximum time in which these temperature and pressure conditions need to be reached with the supplier, thereby optimising the productivity we expect from our autoclave. These data are essential when comparing and matching different pieces of equipment and choosing the most suitable one for our process.
The variety of the different rubber vulcanisation cycles means that there are a large number of different types of autoclaves:
The autoclaves for vulcanising rubber manufactured by Olmar (called ‘ATV’) are not only notable for their high level of technological development, but also for their reliability and durability, which ensure the best performance and highest levels of efficiency throughout their useful life. The application of rubber in increasingly critical manufacturing elements has brought with it an exponential increase in the demands for testing the control, fatigue and measurement of this equipment. Only the most advanced autoclaves are capable of ensuring the levels of homogeneity and cycles required by the industry, which is why it is increasingly important to invest in R&D and constantly improve them.
In this sense, since it started its activity in this sector (the company represented Uniroyal in Spain for more than 15 years in the 1970s), Olmar has dedicated a large part of its resources and R&D to researching the possibilities of these new materials, and has become a national and international benchmark in their study and industrial application.
- Dimensions: Olmar offers autoclaves with a useful Ø diameter from 500 mm to 10,000 mm, and lengths from 1,000 mm to 60,000 mm.
- Maximum working temperatures and pressures (up to 482ºF) and 21 BarG (300 psi)
- Materials: carbon steel, stainless steel or a combination of dissimilar materials
- Layout: horizontal or vertical
The most common steps to follow during a vulcanisation cycle are as follows:
1 / Heating and pressurisation
The means of heating and pressurisation to be used inside the autoclave depend on the nature of the rubber to be vulcanised and its purpose, and there are four main modes:
- Direct steam: by directly feeding saturated steam into the autoclave chamber (Olmar is also a leading manufacturer of steam boilers, with more than 1000 references worldwide and >75 years of experience). In these cycles, pressurisation can be correlated to the temperature of the steam, or carried out independently by feeding in compressed air.
- Indirect heating by means of feeding in steam or thermal oil: in a heat exchanger inside the autoclave, recirculating the hot air inside by means of a turbine and its motor. In this case, pressurisation is carried out independently by feeding compressed air into the autoclave. The use of hot air instead of steam avoids the rubber coming into direct contact with steam, thereby minimising the infiltration of moisture and achieving better adhesion of the vulcanised rubber.
- Indirect heating by means of electrical resistance, recirculating the air inside the autoclave by means of a turbine and its motor. In this case, pressurisation is carried out independently by feeding compressed air into the autoclave. The use of hot air instead of steam avoids the rubber coming into direct contact with steam, thereby minimising the infiltration of moisture and achieving better adhesion of the vulcanised rubber.
- Mixed heating with direct/indirect steam: an autoclave developed by Olmar that can work with the best of both technologies at all times, depending on needs.
2 / Stabilisation phase
Once these target conditions (working temperature and pressure) have been reached, they must be kept there for the minimum time set during the stabilisation phase, which is fully automated thanks to the OCS (Olmar Control System) control system equipped with Siemens or Allen Bradley PLC technology.
3 / Cooling
As in the heating phase, the means of cooling and depressurisation to be used inside the autoclave depend on the nature of the rubber to be vulcanised and its purpose, and there are three main modes:
- Natural cooling: the autoclave cools down naturally as the steam is extracted from inside the autoclave. In some cases, it is necessary to compensate for this depressurisation by feeding in compressed air to ensure an optimum product finish.
- Cooling by means of shower or spray: the autoclave is cooled by water fed from the top of the autoclave and sprayed on the product by means of a shower or spray.
- Indirect cooling: this system is based on feeding cold water into a heat exchanger inside the autoclave, and recirculating the air inside the equipment by means of a turbine and its motor.
Types of cycles for vulcanising tyres
1 / By means of direct steam
Once the autoclave has been loaded, pressurised saturated steam is fed in, subjecting the tyres to the programmed temperature and pressure conditions.
2 / By means of indirect heating
In this type of cycle, each tyre is encased in an “envelope” (layer of rubber) which, in turn, has a valve through which compressed air can be fed in to pressurise the tyre.
Once the autoclave has been loaded, the hoses are connected to the envelopes so that they can be pressurised during the cycle.
As explained above, in this case the hot air is obtained by recirculating steam or thermal oil in a heat exchanger, or by means of electrical heating elements. As the internal temperature rises to 125°C (290°F), the envelopes with the tyres inside are inflated and pressure is fed into the autoclave (with a difference of 2.1 BarG (30psi), until the chamber reaches a pressure of 5.5 BarG (80 psi) and the tyres reach 8 BarG (115 psi).
At this point, the envelope covering the tyre is pressurised to 4.2 BarG (60 psi.). This pressure is generally referred to as “third pressure” and ensures optimum bonding and a better finish on the tyre.
This part of the process usually lasts approximately 120-150 minutes.
Once the above stages have been completed, depressurisation is carried out in the following order:
- Third pressure
- Tyre pressure
- Autoclave pressure
The intelligent autoclave - revolutionary control software
Precision and reliability are key factors in the glass manufacturing process. All of the processes that take place inside the autoclave must be closely monitored and controlled due to the high levels of demand in the automotive and construction sectors. In this sense, Olmar has developed the most advanced software in the world for autoclaves for laminating glass, thereby fulfilling its objectives of digitalisation and efficiency in manufacturing processes. New Olmar autoclaves are, in short, intelligent autoclaves capable of automatically controlling the pressurisation with air, the heating ramp rates of these fluids using electric batteries, thermal oil or steam, the maintenance of vacuum, pressure and temperature values (thermocouples) during curing, and the subsequent cooling and depressurisation, thereby making it possible to control and configure each of their phases. All of this makes it possible for us to produce completely transparent glass, with optimum PVB creep and relaxation parameters that are always in line with the most demanding market standards.
It is not only important to monitor and analyse these values (pressure, vacuum and temperature) during the cycle, but also after the cycle. It is possible to identify potential areas for improvement and optimise the cycle as far as possible by studying all the data collected during the process carried out inside the autoclave. By means of a control system, which was fully developed by the company’s electrical and software departments, Olmar is able to offer its customers optimised performance and, through its innovative reporting technology, the most accurate control and data analysis system on the international market, making a firm commitment to developing the so-called ‘Industry 4.0’ and applying all of the innovative features available in its autoclaves.
Olmar has focused its efforts on creating an “intelligent” autoclave, concentrating its efforts in the fields of energy efficiency, usability, predictive control and low maintenance.
Its OCS control software integrates all of these features, thereby reducing the autoclave’s consumption costs, improving its productivity and optimising any periodic maintenance tasks that need to be carried out. Our technical service provides first class support in any country in the world, thanks to its high degree of connectivity and the incorporation of the most advanced remote connection solutions.
All of this has been embraced in a solid business structure, with a family tradition, yet at the same time flexible and agile, capable of carrying out the entire manufacturing process “in house”; a company focused on a continuous search for innovation and growth. This is demonstrated by its new ‘’cold additive technology‘’ division, a revolutionary concept stemming from our investment in R&D.
Olmar steam generators
Olmar is the world’s leading manufacturers of autoclaves for rubber. This leadership is primarily based on a combination of traditional and innovative engineering and in-depth knowledge of both autoclaves and the processes involved.
In this field, Olmar also has a significant advantage over its competitors: its knowledge and production capacity of steam generators, with more than 1000 references and 50 years of experience.
We recommend that you visit our section dedicated to “Steam Boilers”, where you will find the different ranges of boilers that we manufacture, with production ranges from 100 kg/h to 30,000 kg/h.
Olmar is also able to offer its customers the option of a “turnkey” solution that includes all of the auxiliary systems that complement the autoclave / steam generator for vulcanising rubber:
- Manual, semi-automatic or automatic loading systems.
- Silencer for low noise emissions during depressurisation
- Hardware and sensors for monitoring processes
The possibility of selecting a single supplier, both for the autoclave and its auxiliary equipment, makes it easier to communicate about and integrate all of them, and increases the likelihood of success in the end result of the project.
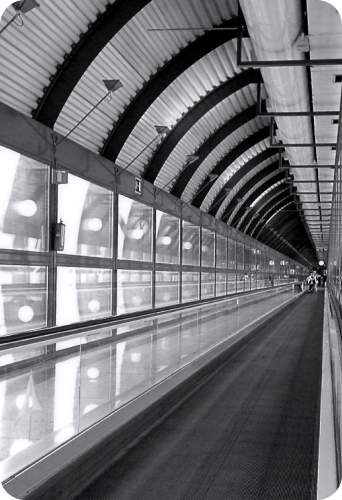
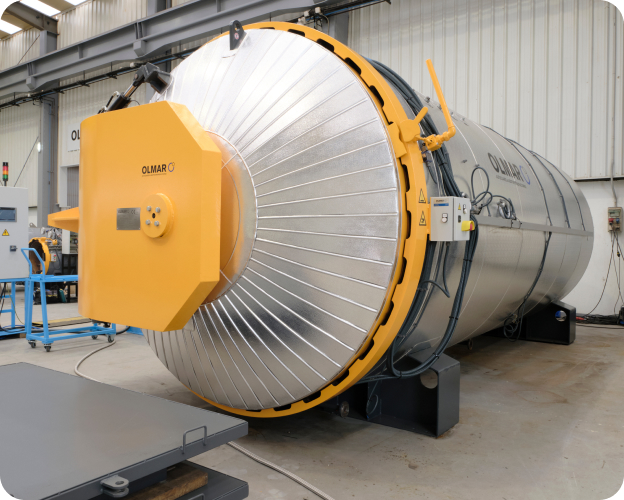
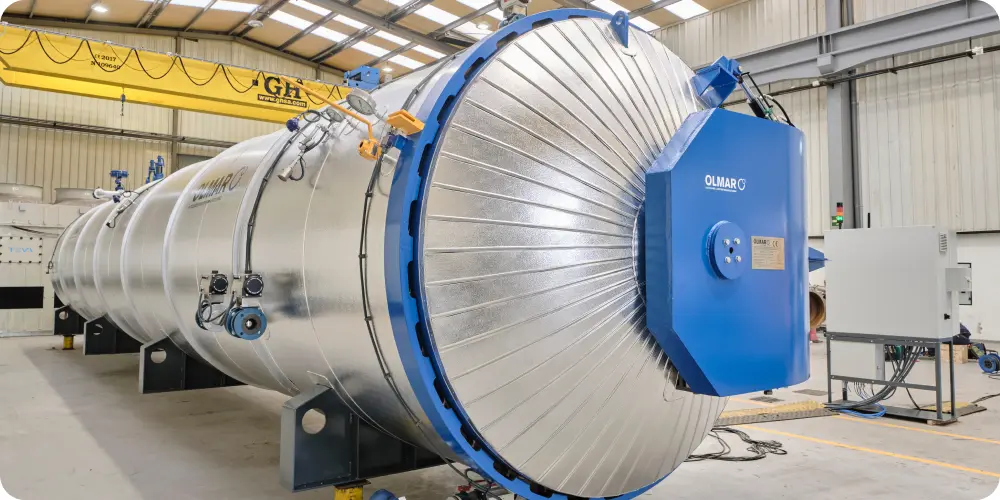
Heavy and passenger vehicles in the automotive sector: the main sector that uses autoclaves for vulcanising rubber
The company’s experience, backed by thousands of international references and top tier customers, has grown over the years based on values such as excellence, effort and constant innovation. Top companies such as Michelin, Bridgestone, Continental, Siemens and Hutchinson, among many others, have put their trust in Olmar autoclaves to undertake some of their most important projects, with products that provide the most advanced solutions for sectors such as the automotive industry, electrical energy, etc. Proof of this is the large number of processes in which Olmar autoclaves and control systems are used and have been integrated.
Olmar is involved in all of them, actively taking part in current, disruptive projects that will change our future, bringing effort, excellence and innovation to technological solutions for manufacturing autoclaves for vulcanising rubber that have never been seen before. Our OCS control software, which is currently considered to be the most advanced application for treating rubber, has made Olmar a point of reference internationally in an increasingly competitive world market.
The increase in consumption and production of tyres are undoubtedly upward trends, defining a market in which the individual turnover of some of these large companies is in excess of 20 billion euros.
Olmar is a trusted partner for this challenge in any country in the world today.
References worldwide
The presence of more than 1500 Olmar autoclaves in 150 countries is a success story and a legacy that has been passed down from generation to generation (today, Olmar is a fourth generation family business).
This can all be combined with the latest international manufacturing, procedural and quality certification, with CE (Europe), ASME (America and Asia), SELO (China), JIS (Japan), etc certifications, among others.
The future - a new generation of autoclaves
In this promising scenario of growth and new challenges, Olmar has consolidated its position as a world leader, presenting its equipment and technological solutions as a guarantee of the highest quality and efficiency when it comes to tackling the industry’s challenges in the coming years. Thanks to the experience acquired over its 75-year history and a team of highly qualified technical experts, the company is looking to tackle these new challenges with the security and confidence necessary to respond to the needs of its customers all over the world.
This can all be combined with the latest international manufacturing, procedural and quality certification, with CE (Europe), ASME (America and Asia), SELO (China), JIS (Japan), etc certifications, among others.